Media error: Format(s) not supported or source(s) not found
ดาวน์โหลดไฟล์: https://www.minnotec.com/th/wp-content/uploads/2022/03/cover-who-we-are.mp4[Case Studies] Work efficiency increased by 40% through machine networking
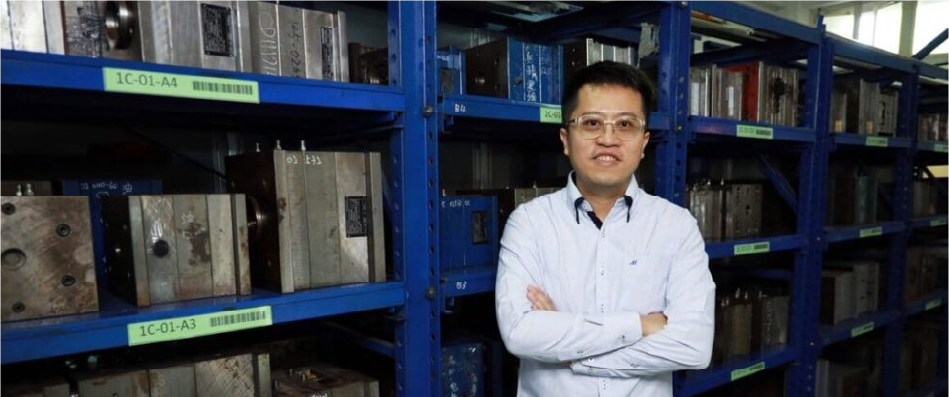
100 Billion Precision Industry Co., Ltd. (hereinafter referred to as 100 Billion Precision) has been committed to the design and development of molds since its establishment. It has accumulated 20 to 30 years of mold development experience, and can meet customer needs in terms of structure and precision. . After the establishment of the plastics department, more attention was paid to the importance of Design for manufacturing in the design of molds. The design factors that facilitated production were taken into account in the early stage of design, and early coordination with customers was carried out. The developed molds are more convenient for production, reduce the defect rate, and even The benefits of reducing manpower can be achieved.
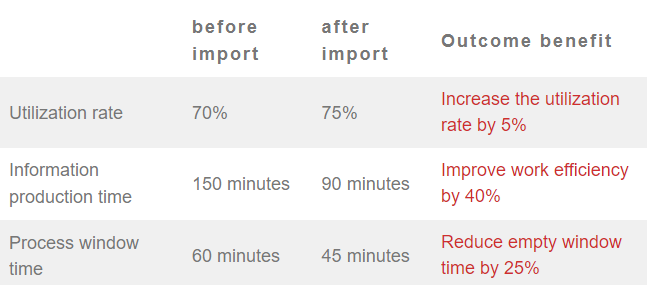
In the early days, Ten Billion Precision started with the development and manufacture of molds. Since most of the customers served at that time came from plastic molding factories, they interacted well with customers in the long-term cooperation process and gradually accumulated their own customers. Therefore, in 1999, they entered the field of injection molding, The initial 6 injection molding machines have grown to 18, which are the following horizontal and vertical machines. They mainly produce small and medium-sized products. The plastic molding application categories include card products, electronic communications, and medical equipment. Mold making and plastic injection.
Ten billion Precision meets customers’ requirements through “exquisite management and soft power”, upholds professional technology, a pragmatic concept, and an attitude of excellence to serve customers, and uses customers’ opinions as an indicator to improve “high-quality quality, customer satisfaction”, And with a refined management model to reduce the cost of management and sales, and give back to customers; and in 2012 obtained the ISO 9001 quality system certification.
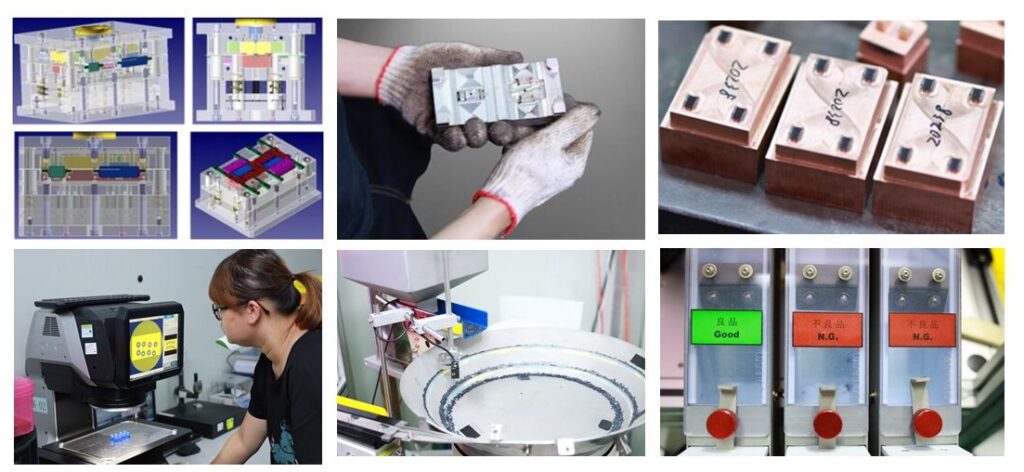
Initiate device networking, the first step in digital transformation
For manufacturing factories, many production operations still require human work records. The process of manually copying and tracing orders is often time-consuming and not immediate, and there is a gap with the actual situation. In the past, the way of factory management data was a manual inspection of key-in, which often took a lot of time and was inefficient. Whether it was a manual operation or personnel information transmission, it took a lot of time, and it took a lot of time for managers to find out when they were checking the report. Abnormal times are often a foregone conclusion, and management is ineffective. For the factory, it is very important to grasp the progress of the order production. When there is a gap between the expected and the actual production situation, it will cause too much production or insufficient quantity, resulting in the need to reload the mold and cause a waste of time, which is very important to the factory. loss.
Therefore, it is necessary to carry out the first step of digital transformation, start the equipment networking, and use the technologies of the Internet of Things and the Internet of Machines to achieve the connection between the injection machines in the factory and the application of system integration, so as to make the traditional injection molding manufacturing industry intelligent and intelligent. It is a big step to make the production status of the production line and the operation status of the machine transparent. Only through systematic big data analysis to achieve informatization, real-time, and visualization, can we better grasp the “people, machines, materials, methods, and environment” within the factory and find the most appropriate management decisions.
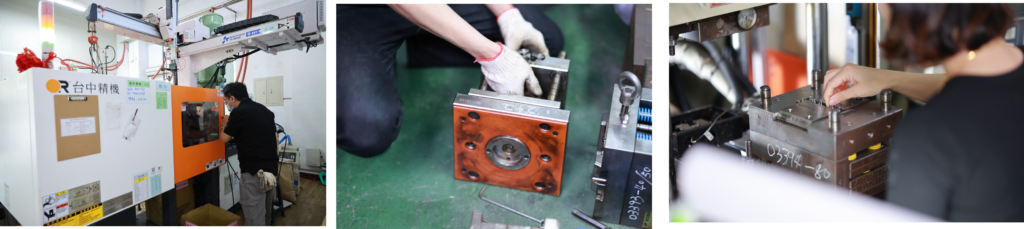
In the face of fierce market competition, traditional manufacturers also face many challenges. When the information is opaque, in addition to the inability of personnel to accurately control the production status of equipment, subsequent capacity analysis, such as equipment utilization rate data, capacity status, Abnormal state, etc., is difficult for managers to have reliable information for process improvement. In participating in the annual meeting held by ACMT, I learned about the IoM (Internet of Molding) machine networking solution, which is simple and fast to install on any brand of the injection molding machine. Capture the data of the injection machine through the smart set-top box to provide analysis and records of equipment utilization, production efficiency, and product yield. You can grasp the real-time status of the factory through a browser or mobile device anytime and anywhere.
In order to effectively improve the unnecessary manual operations in the factory, such as manual meter reading, manual inspection, and many other repetitive operations, it was decided to cooperate with the Model Innovation team, and with the assistance of the Model Innovation team, the machine network was introduced to complete the real-time monitoring of production in the whole factory. The production status of the line (including equipment operation and output), through data-based record tracking, can further revise the plan and grasp the actual situation and have the opportunity to move to the next level for the arrangement of future orders and the management of the factory.

Through the machine network, master the real-time status of the factory
Before importing, it is impossible to grasp the data. In the past, people could only view the device status by switching from one angle to another through the monitor, which was not easy to manage. After completing the visualization of the equipment of the whole factory, no matter where people are, they can instantly grasp the order progress and utilization rate through mobile devices or visual dashboards, and can more clearly grasp the various data indicators in the factory. The problem of data is easier for managers to judge management, and it is easier to track the production capacity even when chasing orders. The demand for digitalization in the general environment continues to increase, and the customers of customers also have this demand. In addition, the IoM (Internet of Molding) system automatically collects production data to monitor the real-time status of machine equipment, adjust the capacity configuration and replace ineffective capacity, so as to make the factory planning more complete. In addition to being more convenient for managers to view, the field personnel can also control the machine status in real-time and adjust the machine utilization rate.
The benefits of this case are summarized as follows:
Office
Minnotec Thailand Co.,Ltd.
Kanya Building (A4)
999 Soi King Kaew 17, Ratchathewa Subdistrict, Bang Phli District, Samut Prakan 10540
Line official
@940ovfau
Contact number
+66 2 - 118 - 2586 (TH)
ACMT Thailand
ACMT Global