Media error: Format(s) not supported or source(s) not found
ดาวน์โหลดไฟล์: https://www.minnotec.com/th/wp-content/uploads/2022/03/cover-who-we-are.mp4[Case Studies] Using the Internet of Machines to Improve Equipment Utilization Rate
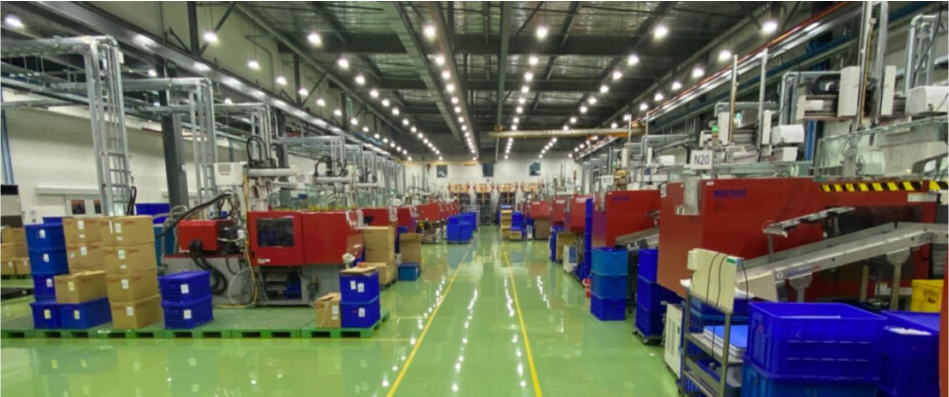
Foreword
Due to the global epidemic, other factories in the world have been shut down, and Taiwan has become a blessed place for continuous operation and supply. Therefore, the client has transferred production orders from other places to Taiwan. Although the orders have grown, the production process rate of the factory remains high. The problem The reason is still not clear. Part of it is also caused by the lack of real-time and inconsistent information, so there are often gaps in information communication, an inability to improve efficiency, and an inability to grasp the status of the entire plant.
This article will introduce readers to the case of Taiwan IDEC (IDEC) based in Kaohsiung, which also faced the above-mentioned problems. In this regard, they chose to introduce a machine networking system in order to solve the problem, thereby bringing benefits such as improving production efficiency and reducing production costs for the company.
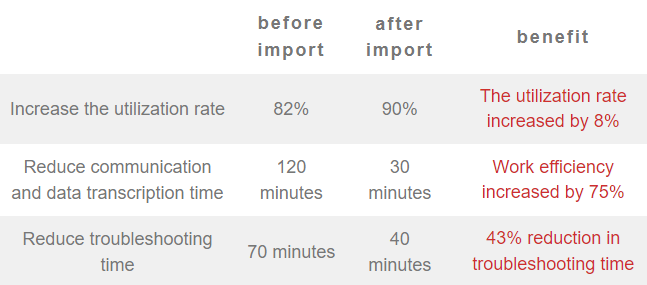
Challenges and responses
The challenges faced in this case are “opaque information cannot be delivered in real-time”, “high cost of the production process”, and “slow processing of exceptions”. Since the traditional injection molding equipment does not have the function of networking, in addition to being unable to effectively grasp the utilization rate, it will also be affected by people, resulting in the situation that the information is not transmitted in real-time or is incorrect, resulting in losses. Faced with these challenges, the first step taken by IDEC Taiwan was to initiate the deployment of the Internet of Things.
Case study
Taiwan IDEC has introduced the Industrial Internet of Things and the Internet of Injection Machines. Through “real-time machine status monitoring”, “process stability monitoring” and other application technologies, machines from different brands, different models, and even different generations in the factory are available. The ability to connect, make information transparent, reduce errors, and free up time for more value-added business matters.
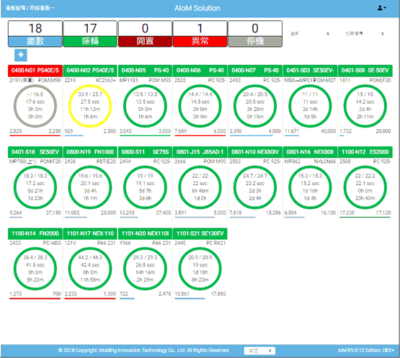
In the past, personnel had to go to the site in person to confirm the operating status of the equipment. It took 120 minutes a day, which was time-consuming and labor-intensive. In addition, because the information was not transmitted in a timely manner, it was easy to cause inconsistencies in information, resulting in a communication gap between personnel. Now, the operation data collection of the injection machine through the smart set-top box has changed from the original manual supervision method to the system automatic collection. In addition to monitoring the idle state of production, it can also statistically analyze the data to find the idle interval, which only takes 30 minutes. It can effectively reduce the time for processing production information and improve work efficiency by 75%.
In traditional factories, when equipment is shut down due to failure because it cannot be found and processed immediately, the production capacity is wasted during the downtime, and in severe cases, it may even affect the delivery due to insufficient production capacity. However, these problems will be solved one by one after the introduction of the injection machine network. For example, when the equipment fails, the system will report it in real-time, so that the on-site master can immediately find the equipment problem, and arrange personnel to remove the obstacle the first time, reducing the average time of problem-solving by 43%.
In the past, when a problem occurred, although it could be solved step by step according to the instructions of the master, it was impossible to grasp the complete information in real-time. And after importing the visual dashboard, it is clear at a glance which device is idle. In addition, managers can quickly learn from the kanban which delivery time is shorter and need to send people to solve the problem first. At the same time, through the kanban, you can also know which equipment order is about to be completed, and you need to prepare to change the mold to avoid a large amount of inventory, so that the next order can be put into production earlier, completed earlier, and moved towards a high-efficiency factory.
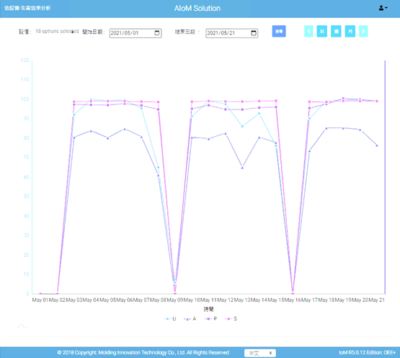
Result
Taiwan Aidac has completed the network deployment of 18 cross-brand injection molding machines. With the data analysis function of the Internet of Molding (IoM), the required information and data can be obtained quickly and in a focused manner, which satisfies the needs of the client and large To meet environmental requirements, it is possible to remotely monitor on-site production conditions in real time, including utilization rate, time utilization rate, production stability rate, and completion measurement. System data analysis can help track historical production conditions, quickly understand problem points, and further solve problems. Through the introduction of machine networking, the benefits brought are as follows:
- [Increase the utilization rate of equipment] from 82% to 90% (the utilization rate increased by 8%)
- [Reduce communication and data transcription time] from 120 minutes to 30 minutes (work efficiency increased by 75%)
- 【Reduce troubleshooting time】from an average of 70 minutes to 40 minutes (43% reduction in troubleshooting time)
It can be seen from the above cases that the establishment of the Internet of Things for equipment allows remote monitoring of on-site status, and the introduction of intelligent set-top boxes such as injection molding equipment to achieve factory visualization, real-time, and uniformity, and make the traditional injection molding manufacturing industry towards intelligent and intelligent manufacturing. Take a big step to help customers build a digital chemical factory, instantly grasp the on-site situation, grasp the status of order completion, effectively reduce management costs and grasp the status of the factory, and deeply experience the enhancement of industrial competitiveness brought about by digital transformation.
Office
Minnotec Thailand Co.,Ltd.
Kanya Building (A4)
999 Soi King Kaew 17, Ratchathewa Subdistrict, Bang Phli District, Samut Prakan 10540
Line official
@940ovfau
Contact number
+66 2 - 118 - 2586 (TH)
ACMT Thailand
ACMT Global