Overview of Moldex3D Plastic Mold Flow Analysis Solutions
Moldex3D is the leading brand of CAE mold flow software in the global plastic injection molding industry. With the most advanced real 3D simulation analysis technology, it helps users in various industries around the world to solve various plastic product design and manufacturing problems, shorten the time to market, and achieve product Profit maximization. Moldex3D fully provides the different analysis tools required for each stage of the design chain. The eDesign series is a complete set of product and mold design tools, which is convenient for mold designers to quickly verify before mold processing. Professional and Advanced are high-level plastic injection molding engineering analysis and optimization software, providing in-depth and complete analysis functions for various advanced processes.
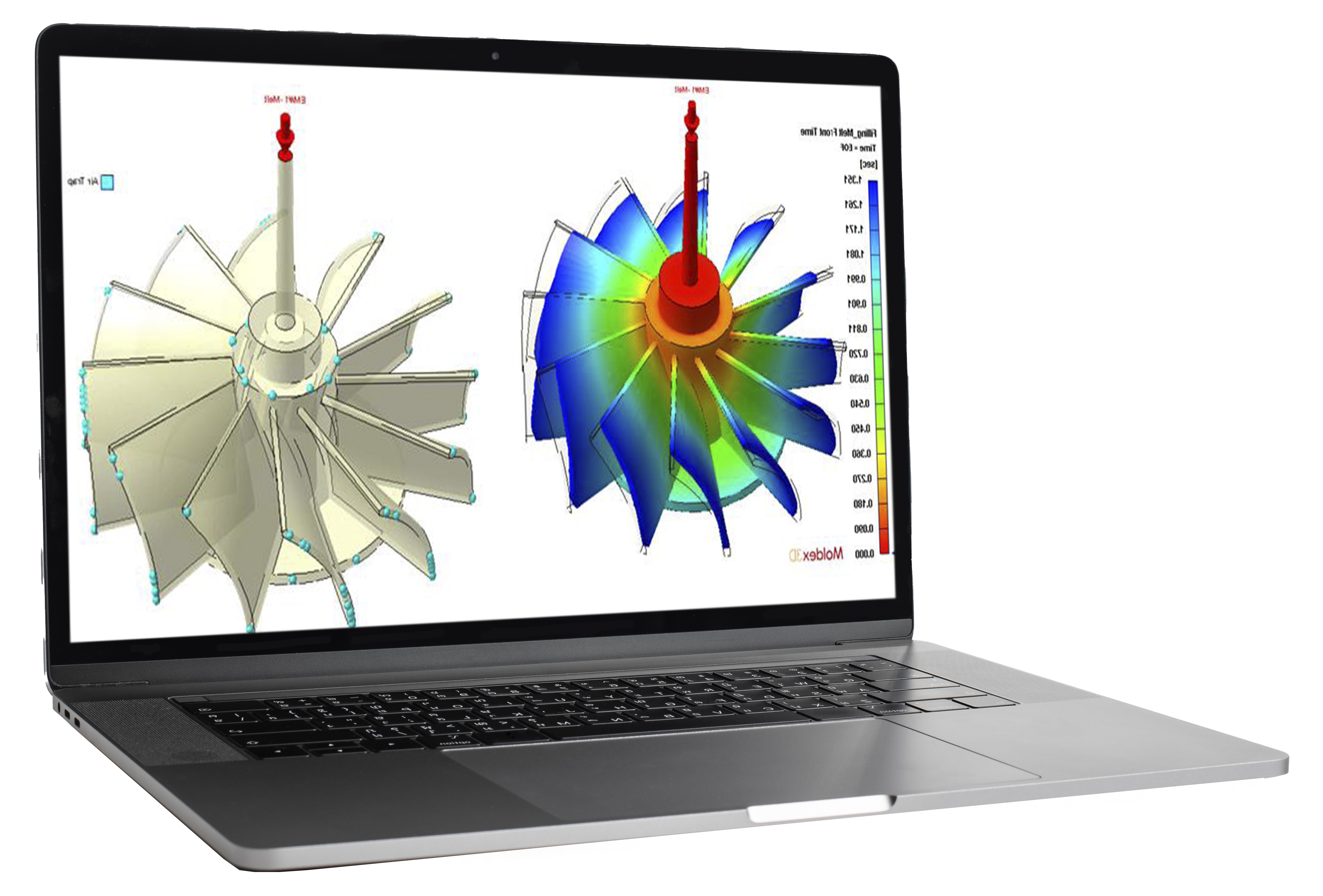
Mold & Part Simulation
To the manufacturing industry, molds are equivalent to the heart of a company. Without a good mold, various problems can occur during the injection molding process causing parts to have defects. Some of the common problems include warpage, short shot, air trap, shrinkage, weld line, burn mark, and much more. Oftentimes, companies look for quick-fix solutions to “modify” the defective parts so they still are deemed acceptable to the customers. However, these would incur a huge cost cumulatively without ever eliminating the problem from the root cause. With the power of simulation, we can now predict these problems before making the mold to eliminate the problem using an upstream approach. This approach can help not only reduce trial time, material waste, labor cost, but also maintain stability and the quality of production.
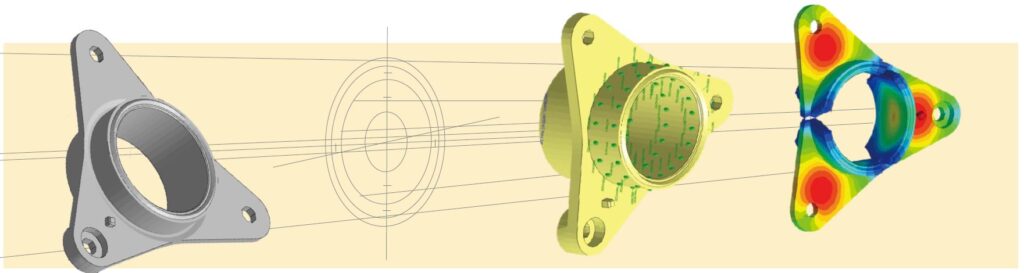
Moldex3D Mold Flow Analysis Software – Product Features
– Comprehensive and integrated analysis capabilities
– Powerful automatic 3D mesh construction engine
– High-Resolution Boundary Mesh Technology
– Efficient multi-core and parallel computing technology
Moldex3D Mold Flow Analysis Software – Successful Case
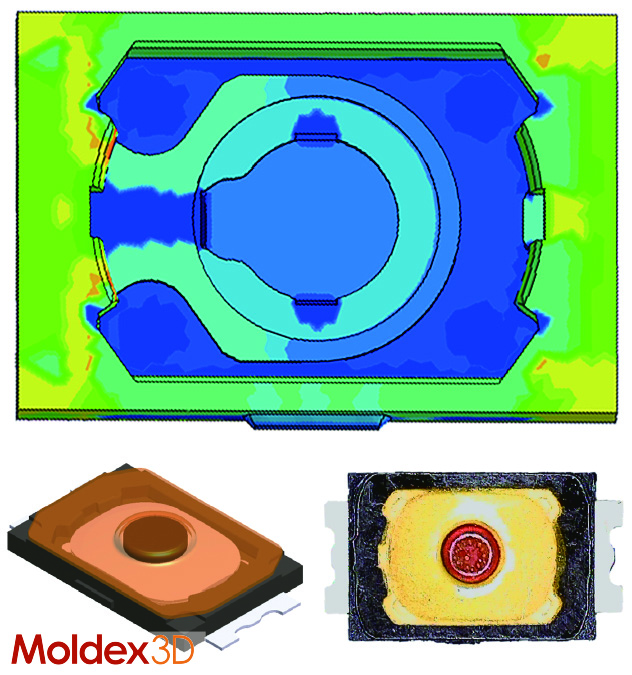
Tutored unit: Wonda Industry
T3C light touch parts are one of the products with the highest output in Wonda electronic switches. The main purpose of electronic switches is to touch the switch to make the circuit conduct . Lines , lack of materials and other problems, resulting in poor conduction of the product.
solution
Use Moldex3D to analyze and change the position and direction of the runner, and improve the appearance defects by increasing the overflow area and changing the design of the product appearance.
Solution – Benefit
– Effectively control the position of the bonding line
– Improve appearance defects such as packaging and material shortages
– Flow balance
– Reduce residual stress
– Reduce sprue nozzles to save materials
– Shorten molding cycle
– Increase yield by 39.68%
– Reduce production cycle by 16%
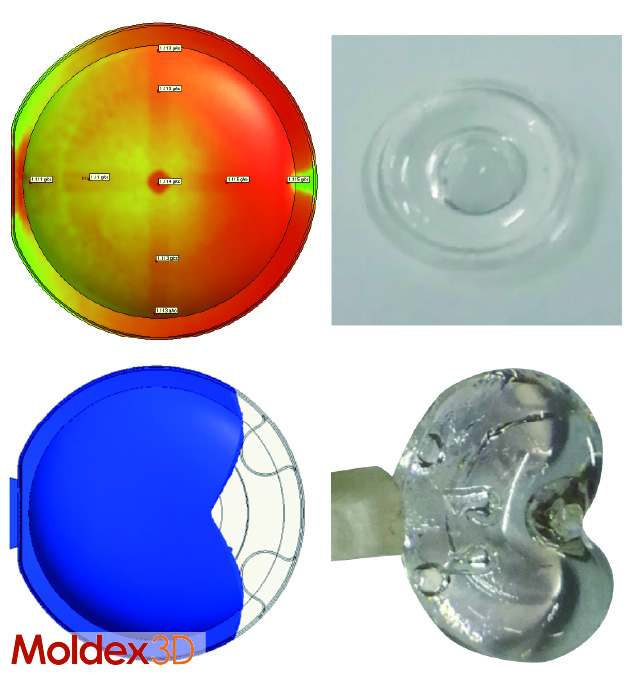
Tutored unit: Xuri Optoelectronics
The optical lens is an important part of the camera lens. There are often 1 to 2 convex and concave lenses on the camera lens module. Under the characteristics of the convex and concave structure, the bonding line generated during injection molding is bound to exist, and the bonding line causes serious damage. Influence, the optical design fails to achieve the intended purpose.
solution
The influence of the pressure field on the flow state of the melt filling was successfully predicted by Moldex3D, and the influence of the bonding line on the imaging of the optical lens was improved.
Solution – Benefit
– Optimized LED lens waterway design
– Eliminates bonding lines and restores the best optical design
– Improves transcripability, increases lens surface density, and increases film strength by 30%
– Optimizes product molding cycle
– Reduces product stress
– Reduces production costs
– Increases Productivity
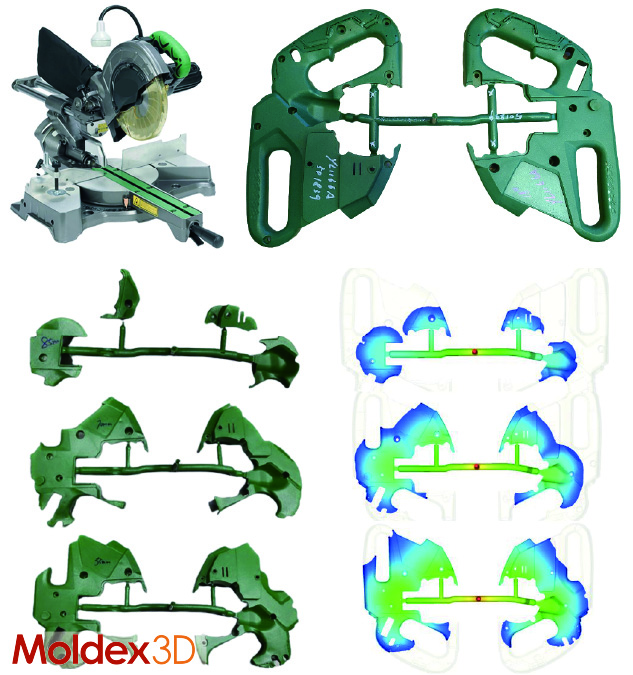
Tutored unit: Haojing Plastics
The product is a composite beveling machine handle for power tools, which is made of PC+15GF plastic and formed with a cold runner. The mold produced is poured at 3 points, and because the material used is very hard after molding, three people are required to process it.
solution
Use Moldex3D BLM for analysis to verify the accuracy of the original plan analysis results, analyze and compare the differences with the original design, and adjust the molding conditions to reduce its deformation and pressure.
Solution – Benefit
– Reduce labor cost by 67%
– Save raw material cost by 33%
– Optimize runner design and molding conditions
– Reduce deformation and pressure, shorten the production cycle
– Reasonably adjust molding parameters and reduce the number of mold trials
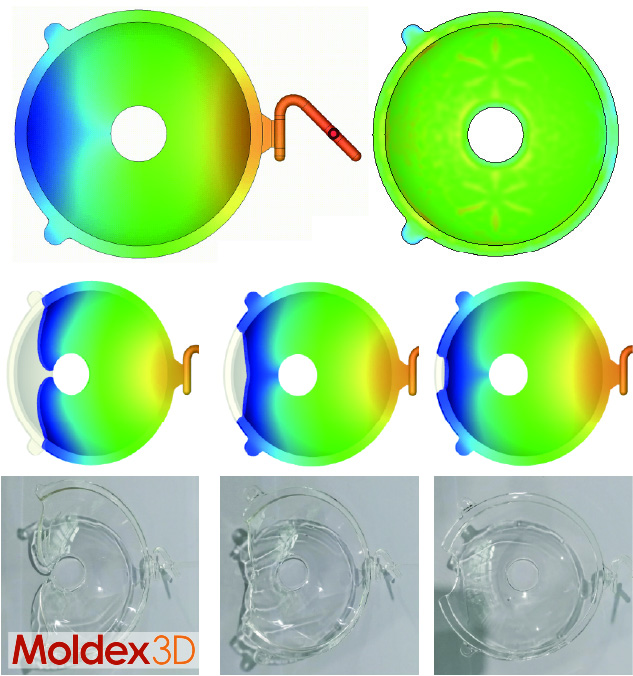
Tutored unit: Dongguan Institute of Technology
Fresnel lens, one side of the lens surface is smooth, and the other side is burned with concentric circles (equidistant tooth patterns) from small to large. Through these serrations, the effect of the light band pass (reflection or refraction) of the specified spectral range can be achieved. Bandpass optical filters for traditional polished optics are expensive to manufacture.
solution
Use multiple modules of Moldex3D to verify the design of ordinary waterway and follow-up waterway many times, and then use Moldex3D to predict the optics and residual stress to further optimize and improve the process, help enterprises reduce production costs, and improve production efficiency.
Solution – Benefit
– Find the best waterway layout scheme to follow the shape to improve the uneven temperature distribution after cooling
– Shorten the product cooling time (15 seconds→13 seconds)
– Effectively control the temperature of the seam line
– Meet the product dimensional accuracy requirements
– Product residual stress is low and uniform
– Optimization Product molding cycle
– Improve production efficiency
– Reduce production costs
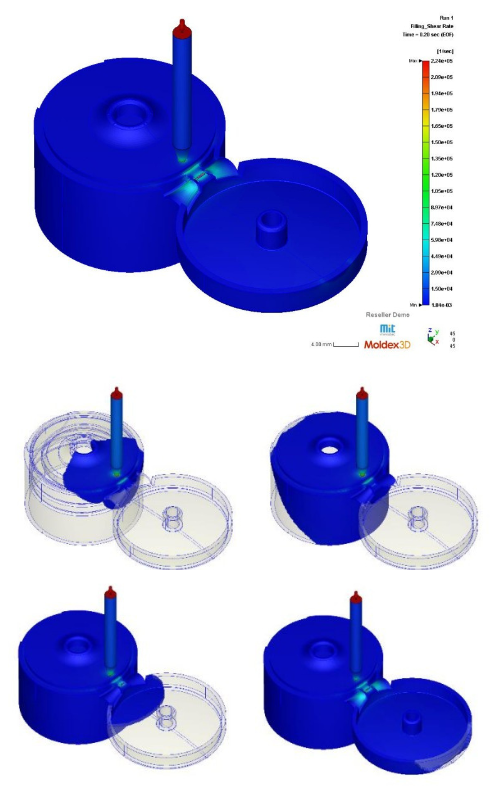
Tutored unit: Minnotec
Flip-top lids are products that focus on applications in the field of packaging, whether in the food packaging industry, cosmetics packaging industry, and ETC.
A common problem with this workpiece is the polymer fatigue caused by the use of opening and closing the lid. These problems arise from the use of high injection molding speeds that cause friction of the polymer as it flows giving the structure of the polymer is damaged which directly affects the strength and The number of times the product is used is shortened.
solution
Used Moldex3D to analyze the shear rate effect generated by injection molding speeds based on the parameters that used in the injection molding process From the study of flow behavior and velocity used in molding, it was found that the use of high-velocity injection molding causes the shear rate to increase, On the other hand, using low injection molding speed, the shear rate will decrease but there will be a problem of solidification of the polymer, resulting in a short shot problem that can follow if the injection is taken too long.
Solution – Benefit
– Reduce shear rate
– Check the shear rate arising from various conditions by simulation
– Model and find the most suitable parameters for injection molding
– Reduce the rate of waste
Certification from Moldex3D
Won the original Master and Junior certification of Moldex3D. For the introduction of Moldex3D professional certification
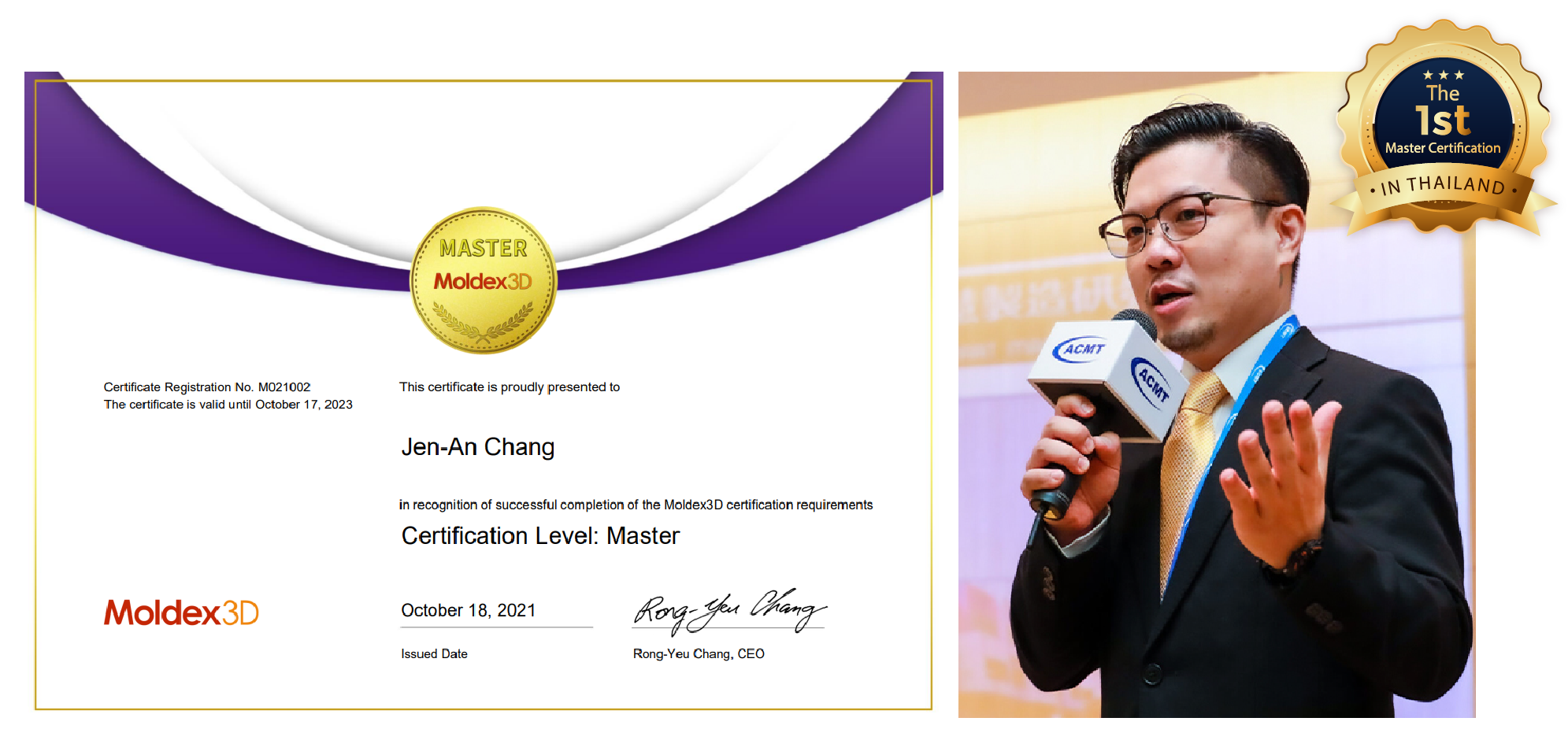
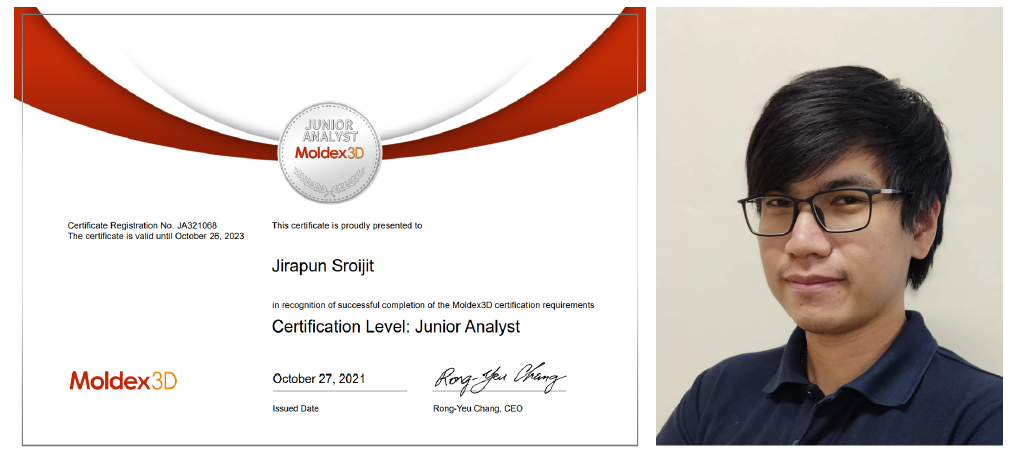
Office
Minnotec Thailand Co.,Ltd.
Kanya Building (A4)
999 Soi King Kaew 17, Ratchathewa Subdistrict, Bang Phli District, Samut Prakan 10540
Line official
@940ovfau
Contact number
+66 2 - 118 - 2586 (TH)
ACMT Thailand
ACMT Global