SOP
SOP (Standard Operating Procedure) is an important principle for the most efficient plastic injection molding process. The SOP principle indicates the appropriate machine size for injection molding for each material type and product shape.
It is also a principle for adjusting the correct injection parameters such as Injection Pressure, V.P. Point, Cushion and Packing Pressure, etc. Which can adjust the injection parameters correctly and appropriately. It will help the production process to be more stable and efficient. The SOP principle can also be used to detect in order to find the cause of various problems that occur in the production process,
for example, the cushioning value in the injection is not consistent due to the checking ring deterioration causing some plastic to flow back into the syringe during injection molding and resulting in unstable production, etc. from such problems If you know the root cause of the problem. This will enable correct and on-the-spot troubleshooting and can also plan to avoid problems in the future.
Therefore, SOP principles are very important for operators in the plastic injection molding industry to upgrade and increase the efficiency of the production process.
Instructors
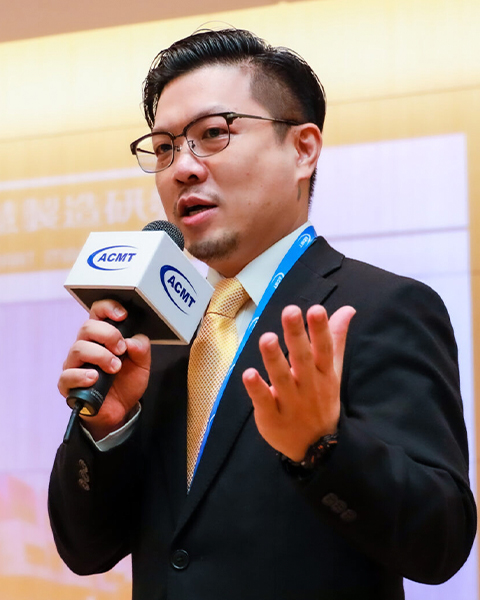
Dr. Jen-An Chang
Expertise
- Advanced injection molding technology
- Industry 4.0 intelligent injection technology upgrade
- Technology upgrade and molding problem diagnosis
- Computer in Engineering Analysis (CAE) Moldex3D Level: Expert
- Mold automation technology and injection molding technology
- Dynamic mold temperature control technology
Success
- Invited by the Thai government. He is the first injection molding technical advisor of the National Science and Technology Development Agency (NSTDA), Thailand.
- 29 injection molding patents
- Nearly 1000 publications referenced to date (Google Scholar)
- Experience in technology consulting for 100 companies worldwide and creating value-added more than 45 million baht
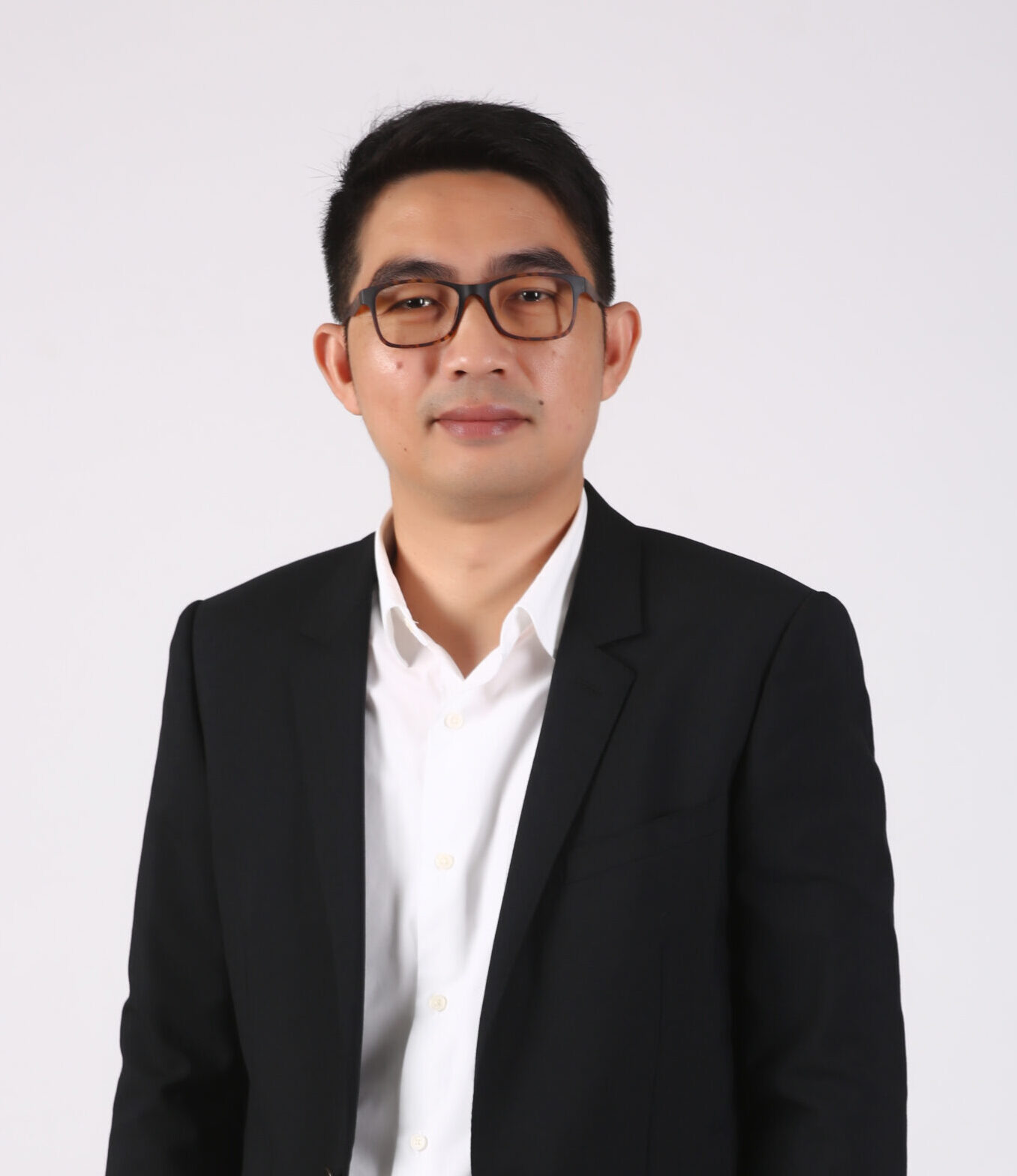
Dr.Sorasak Wongmanee
Expertise
- Mold design technology
- Injection molding technology
- Cutting Tool Technology
- Computer in Engineering Analysis (CAE)
Success
- Engineer, Uni-Tech Mold and Die Industrial (Thailand) Co., Ltd.
- Engineer in Mold and Tool Engineering Technology
- Special Lecturer in Mold and Tool Engineering Technology
- Lecturer in Mold and Tool Engineering Technology
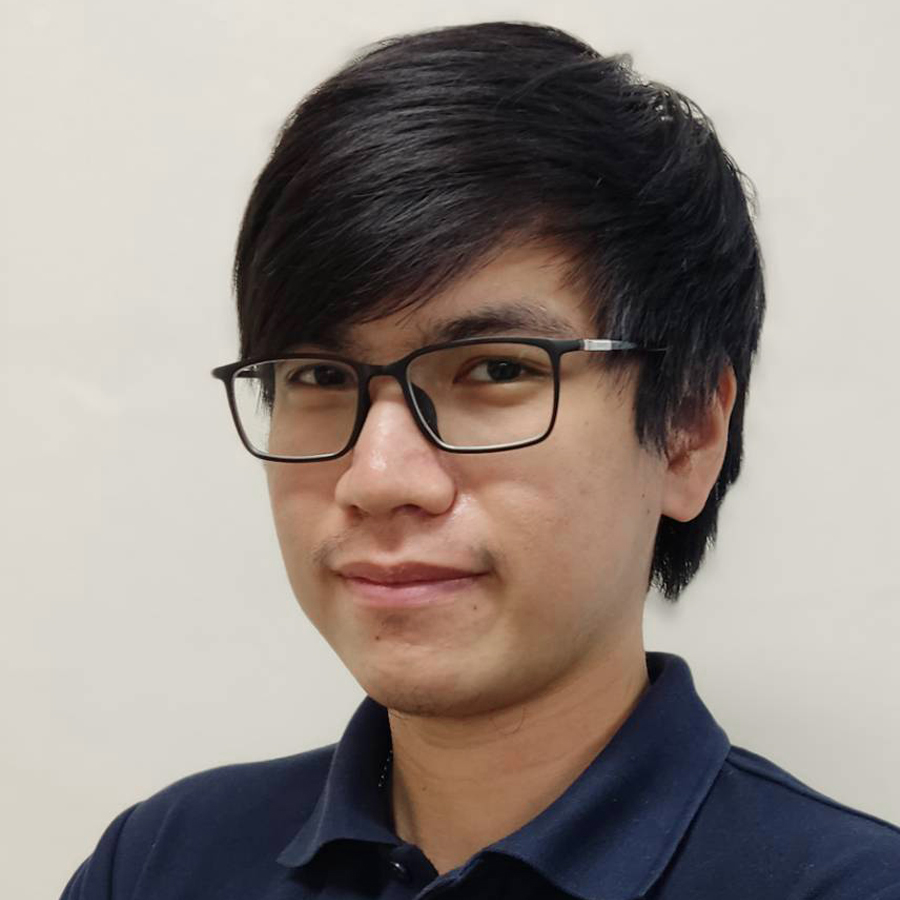
Mr.Jirapun Sroijit
Expertise
- Mold design technology
- Injection molding technology
- Computer in Engineering Analysis (CAE)
Success
- Graduated in Mold and Tool Engineering Technology
- Engineer Minnotec (Thailand)
The exception targets
Optimization of the injection molding conditions.
To get the best cycle time.
To get the best products quality.
To increase the molding yields rate.
SOP table can become the standard in the company for a long time application.
SOP Training Details
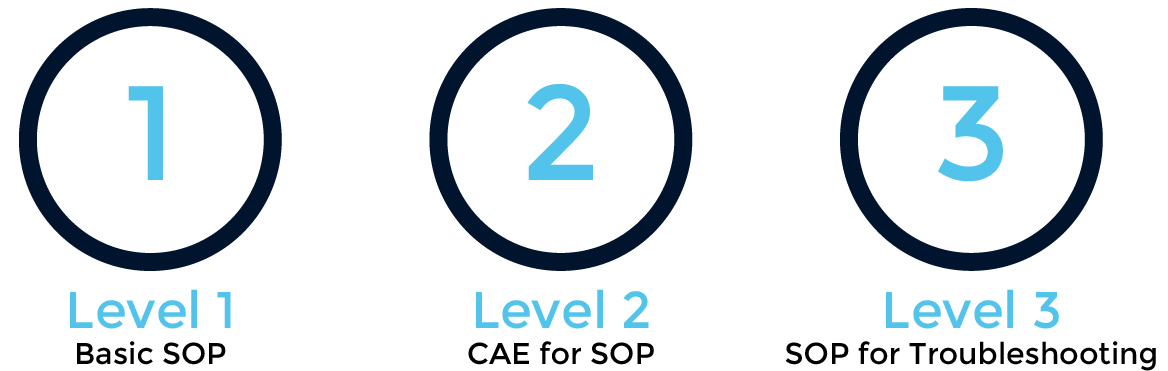
Level 1: Basic SOP
1st Day Program (6 Hrs.)

TOPIC
• Greeting and introduction
• Pretest
• Concept of SOP for Mold Trial
• 11 steps for Standard Operation
Procedure: SOP
• Step 1 Clamping force
• Step 2 Volume (Melted)
• Step 3 Feed stroke
• Step 4 Heater temperature
EXPECTATION TEAM
• Injection molding team,
Mold design team,
process improvement
team
TEACHING METHOD
• Power point and in
house case study
Level 1: Basic SOP
2nd Day Program (6 Hrs.)

TOPIC
• 11 steps for Standard Operation
Procedure: SOP (Continue)
• Step 5 Injection step (Short shot
position design)
• Step 6 U-Curve: Finding Speed
• Step 7 Filling step
EXPECTATION TEAM
• Injection molding team,
Mold design team,
process improvement
team
TEACHING METHOD
• Power point and in
house case study
Level 1: Basic SOP
3rd Day Program (6 Hrs.)

TOPIC
• 11 steps for Standard Operation
Procedure: SOP (Continue)
• Step 8 Packing time
• Step 9 Cooling time
• Step 10 Mold Close, Open
• Step 11 Cycle Time Total
EXPECTATION TEAM
• Injection molding team,
Mold design team,
process improvement
team
TEACHING METHOD
• Power point and in
house case study
Level 1: Basic SOP
4th Day Program (6 Hrs.)

TOPIC
• 11 steps for Standard Operation
Procedure: SOP (Continue)
• Example case in Conimex
• Team’s case study presentaion
EXPECTATION TEAM
• Injection molding team,
Mold design team,
process improvement
team
TEACHING METHOD
• Power point and in
house case study
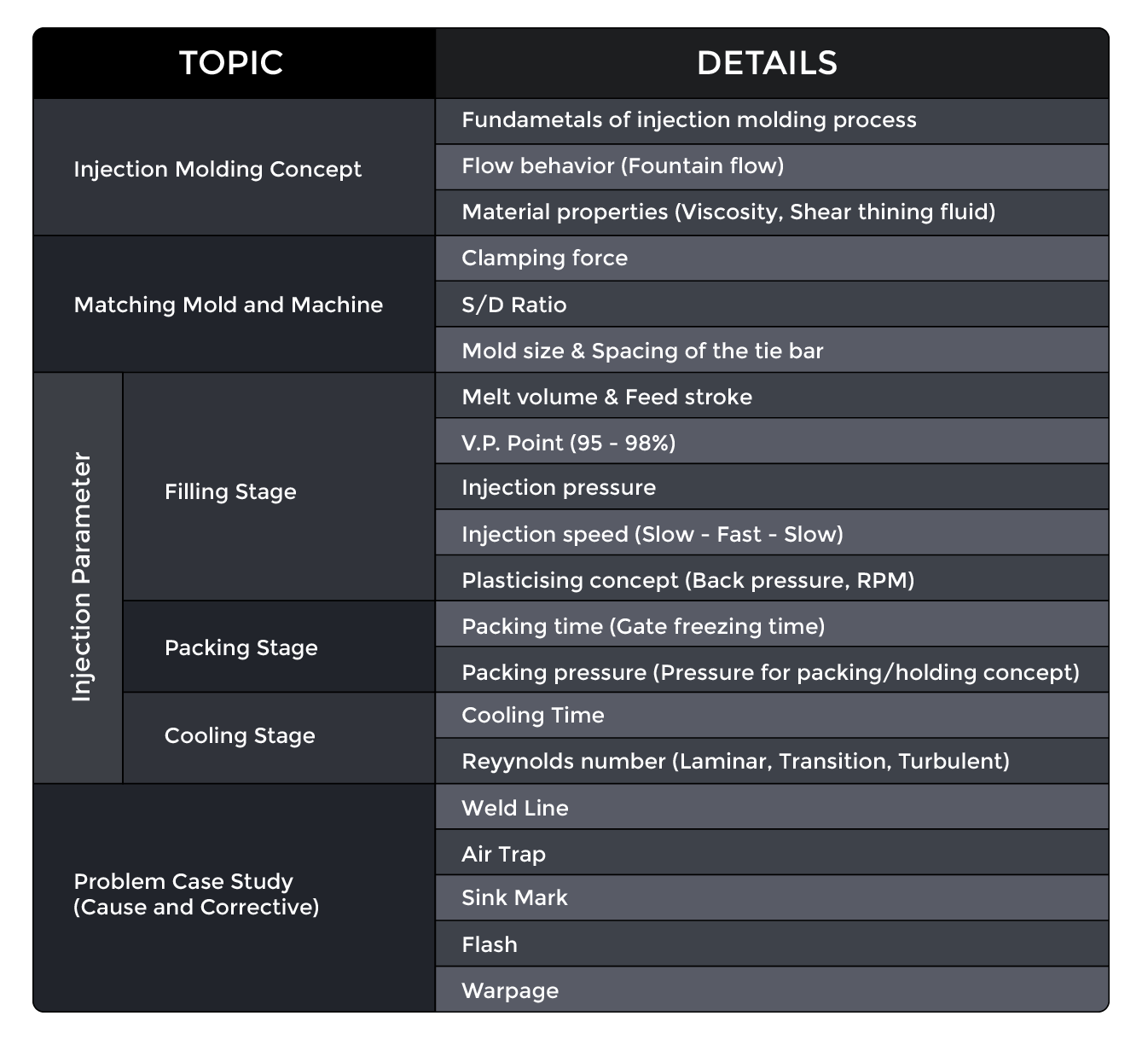
Location
40 Moo 12 Soi Shamit, Sukhumvit 77 Rd., Srisajorakae-Noi, Bangsaothong, Samutprakarn
VIEW MAP
Office
Minnotec Thailand Co.,Ltd.
Kanya Building (A4)
999 Soi King Kaew 17, Ratchathewa Subdistrict, Bang Phli District, Samut Prakan 10540
Line official
@940ovfau
Contact number
+66 2 - 118 - 2586 (TH)
ACMT Thailand
ACMT Global