型創科技 / 劉文斌 技術總監
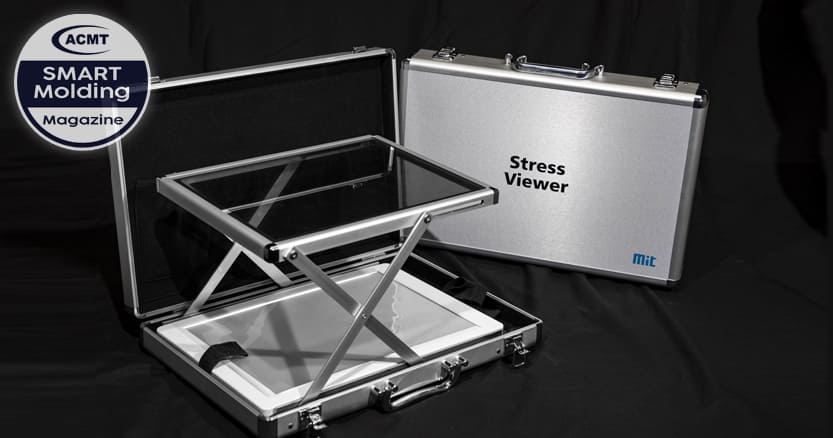
前言
當塑膠成品在應用上發生破裂或破壞時,就材料力學的觀點而言,即表示該塑膠件在破壞區域上,其所承受之應力數值總合超過了材料本身的物性強度數值。因此要解決成品在使用上的破壞或破裂問題,就必須要從增加材料物性強度或減少成品應力值來著手。塑膠製品承受的應力作用通常可依應力來源區分為「外部應力」及「內部應力」兩種,「外部應力」是成品在使用時所遭受之外力作用,此部分將視產品應用場合而定(例如塑件使用上遭受碰撞、荷重、嵌合等),通常是無法控制其程度,一般產品設計者會依照常態之外部應力值,乘上一安全係數值來設計產品的結構強度。而內部應力通常是成品在加工成型過程中所產生而留存在塑件成品內部(稱為塑件的殘留應力或成型應力)。所以要有效解決塑膠成品的破壞問題,唯有降低應力作用或提高材料強度兩種方法。
然而對於塑膠成型加工業者而言,如何使用較適當之加工條件,來防止材料強度降低及避免在加工時產生過大殘留內部應力則是現場加工人員最重要的議題。殘留應力就是指在塑膠成型過程中,因加工條件造成分子結構不是處在其最低能量的最穩定狀態下,分子鏈可能是受到流動定向影響或是受到周圍分子鏈之冷卻拘束,而呈現不穩定之高能態狀況。所以一旦有外界能量再度給予此受應力作用的分子鏈具備有足夠的動能,則此分子將極易釋放出應力而達到其最穩定的最低能階組態。塑膠成品中的殘留應力通常難以透過肉眼進行觀察,往往是在進行成品後加工製程時發生了問題或是在使用時產生了破壞,才會被發現,所以塑膠加工成型業者如何在成型階段或是在加工生產線上,藉由成品之觀測來迅速獲得殘留應力的分布資訊,是目前加工上相當重要的技術。
在一般塑膠射出成型加工過程中,由成品厚度方向來觀察,可以發現成品可依分子鏈之微觀結構差異,來區分不同之區域,如圖 1 所示。其中 A 層是固化層,B 層是流動高剪切層,C 層是高溫熔膠流動層;A 層為塑膠充填時緊貼兩側模壁,瞬間冷卻固化的高分子鏈定向層,此部分會因為射出成型之噴泉流場效應(Fountain Flow),而使分子鏈排向方向與流動方向相反,而 B 層是塑膠充填時緊靠 A 層固化層的高剪切區域所形成的分子鏈定向層,由於與 A 層具有最大之速度差,所以會形成最大的剪切流動應力效果,塑膠充填結束時本區定向層尚未完全凝固,而外層之 A 層固化定向層有絕熱效果,使 B 層熱散失不至過快,另外由於高剪切作用會產生剪切加熱作用,所以本區也是在產品厚度方向上溫度有可能是最高的區域。而 C 層因熔膠高溫及有足夠時間來進行冷卻,分子鏈有足夠時間進行分子鏈排向的鬆弛作用,所以最終高分子鏈的定向行為會因為分子鏈鬆弛而消除,是故 C 層區域的高分子鏈彼此之間較無剪切作用現象,若產品厚度有變化,則主要會影響 C 層厚度,若是薄件成品則 C層的厚度將會變小。圖 2 是沿厚度方向分子定向效果分佈情況的示意圖。
除了在成品厚度方向上下表面有一薄層固化層外,大部分區域是屬於熔膠流動層,而這區域主要的內部應力形成是由於不均勻的冷卻造成,塑膠件厚度方向的冷卻作用是由與模壁接觸之成品表面開始向成品內部延伸,所以中心層是最慢冷卻的區域。所以當塑膠成品成型後,開始進行冷卻階段時,在某一特定位置上之分子鏈會受到其較外部端已冷卻收縮之分子鏈牽引,所以會感受到先前已冷卻收縮之分子鏈的拉伸應力。所以嚴格來看,在成品厚度方向靠近上下表面的區域,分子鏈是處在壓縮應力狀況,而內部區域是處於拉伸應力狀況。圖 3 是射出成品厚度方向應力分佈情況示意圖。
殘留應力的影響
塑膠成型過程所產生的殘留應力,除了會影響成品在使用上的強度外,尤其在某些二次後加工製程上(例如噴塗、電鍍等)都會容易造成產品不良現象發生。殘留應力對塑膠成品的影響常見的有下列幾種:首先是成品的外觀尺寸變形及翹曲問題,由於剪切流動造成分子鏈的排向或是由於成品幾何造成流動的定向效果,在成品脫模時容易因應力鬆弛而造成尺寸發生變形,另外由於成品尺寸的不對稱性或在成品厚度方向冷卻收縮的不平衡性,所形成的熱應力都將造成成品在脫模後發生翹曲變形現象。此現象對於尺寸精密度有要求或有組裝搭接嵌扣性需求之塑膠射出成品,將會有尺寸配合度的問題發生。再則塑膠件在使用上比例最高的破壞型式,當屬環境應力破壞 (Environment Stress Cracking,ESC) ──例如太陽 UV 光照射破壞、老化破壞、氣候性乾溼冷熱循環破壞等等,對此塑膠殘留應力也會造成環境應力破壞的加速。其他像塑膠件的蠕變性破壞、疲勞性破壞等,都會因為殘留應力存在而加速加快其破壞產生。
另外,塑膠件在成型過程中所產生的殘留應力,容易因為獲得外界能量或驅動力(例如受熱、照光、吸濕等)來誘發應力鬆弛效果,所以在塑膠成型業中最常用來消除塑膠內部殘留應力之方法,即是退火(或回火、annealing),將塑膠成品放入烘箱中或給予所需熱量,使定向分子鏈獲得能量而能再次重新調整分子鏈組態或相互重排以達到最低能量之穩定結構,而應力鬆弛的驅動力除了熱能外,如機械能、光能、化學能(溶劑作用)都可以達到同樣效果,然而在應力鬆弛的同時,也要考量成品尺寸變形之嚴重性。一般殘留內部應力常常會導致成品在使用上或二次加工上發生問題,例如表面接著、表面電鍍或表面塗裝等工法,都會因為成品表面高度分子定向的高應力情況,而產生介面的不相容性。另外如接觸到溶劑、化學品等也會造成在應力區域的加速劣化。
應力偏光檢測之理論基礎
光的產生是藉由電荷振動所釋放之輻射波,光束同時具有粒子及波動之特性,所以光波可在真空中傳遞,是屬於電磁波之一種。然而由於光可以向四面八方照射,所以若以自然光來做一些如干射、繞射等分光光譜觀測時,將會因為各方向光波的互相干擾而無法辨識。因此為方便於光譜觀測及便於以簡單數學方程式來表示,所以一般常用單方向之光波來作為觀測光源,而所謂單方向光源則是利用將白光光源,通過一單方向之光學偏光片,使其通過之光波都固定在一特定方向上。我們可以簡單拿兩片光學偏光片依前後放置在一白光光源前,當白光通過第一片偏光片時已成一單方向光波,若旋轉第二片偏光片觀察時,將會發現當兩片偏光片成平行時,可見到白光通過;但若兩片成垂直時,則呈黑暗無光線通過。
在有殘留應力存在的塑膠材料中,在特定平面上可將應力分成兩個主軸應力,此不均勻之應力將使材料產生兩個不同的折射率。因此光要通過此材料時,沿二個主軸應力方向振動的光波彼此有不同的速率,穿出材料時,則會有相對速度差產生。而此相位差將正比於平面上的兩個主軸應力之差值。所謂應力光學定律是指當一透明塑膠材料受應力時,其折射率會隨著所受應力變化而改變,當物體的應力狀態和光交互作用,則可藉由光彈條紋來推知物體的應力狀態。光彈性量測應力的方法其主要優點在於可瞭解外力作用瞬間或成型定型後,測試品整體的應力場分佈,可實際用於產品 QC 檢測上。
透明塑膠材料遭受應力時將產生雙折射現象,當光線穿透具雙折射率的材料時,光在材料內進行的速度也會不同。當偏極光進入有應力作用之雙折射材料時,光線會分為較快速及較慢速兩光束,其速度差相對距離則稱為相位差或光程差或遲延 (retardation,R)。在單色光的光彈條紋中(明暗條紋),粗線的地方代表該點之主應力方向與x軸(或y軸)平行。因此兩道光之相位差為整數波長,因而造成光場之明暗條紋,光場之條紋可以肉眼觀察,條紋越密集的地方,表示應力愈大,亦即是應力集中的地方,也是材料較容易發生破壞時最先開始之處,圖 4 是應力偏光儀量測觀察應力之原理,而圖 5 是應力偏光觀測裝置。
應力偏光儀觀測透明塑膠件的殘留應力
對於光電產業常使用的透明性塑膠材料而言,目前最簡易可用來觀察材料內部殘留應力之方法,就是使用穿透式應力偏光儀,來觀測光線通過透明塑膠件後,所呈現之明暗干涉條紋(使用單波長光源)或七彩條紋(使用白光光源),如圖 6 所示。此方法是一種非破壞性的定性觀測方法,主要是利用塑膠受應力作用下之光彈特性,來觀測材料的雙折射率變化情形。此由 Brewster 的光彈性定律理論中可知,對於受應力作用而產生應變之高分子材料,其在空間中對光線的折射率將會有方向性的不同,換言之,也就是說塑膠材料在不同方向所受之應力分量不同,其在這些方向所表現之折射率也會不同,而其折射率之差異會與所受之應力程度成正比。當射出模溫接近或超過塑膠之 Tg 溫度時,可有效消除雙折射現象,此即是由於流動所誘發之分子定向現象,可藉由使用較高模溫使分子有足夠動能及足夠時間來鬆弛分子應力。藉由將透明試片置於兩片正交之偏光板間,可觀察到較無散射之彩色光環,有較多區域呈現黑暗顏色,代表分子結構較無殘留應力存在。
塑膠是由長度很長之高分子鏈所組成,所以就微觀角度而言,在分子鏈平行與垂直方向所表現之物性並不一致,此就是高分子鏈的異方向特性 (anisotropic),然而就整體高分子材料而言,因分子鏈間相互糾結成一團狀結構,所以單一分子鏈之異方向特性將不易被察覺;然而若因塑膠材料在加工時所形成之應力,將造成分子鏈之高度定向作用,則塑膠材料之異方向性將會顯現,利用材料內部應力產生之雙折射率,可用來觀察入射光因前進速度之差異所產生之相位差干涉條紋,藉此來反推內部應力之分佈情形。
圖 7 至圖 9 是一些透明塑膠成品之應力偏光觀測照片。圖 7 是 PC 材料射出平板成品,退火前後之應力偏光觀測。而圖 8 與圖 9 是多種透明性塑膠材料之圓片成品,在有無經過偏光照射時之應力分佈觀察情況,由此可明顯得知不同塑膠對成型應力之敏感性。
結論
所以應力偏光觀測透明塑膠殘留應力技術是一項相當簡易之定性觀測方法,可使成型加工業者在生產線上迅速獲得應力分布的資訊,也可迅速調整成型加工參數的設定,減少成品的殘留應力與減少產生破壞之可能性。
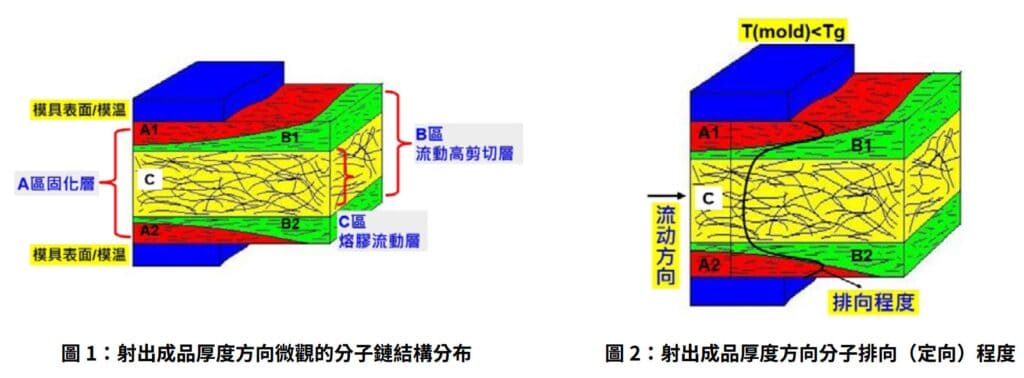
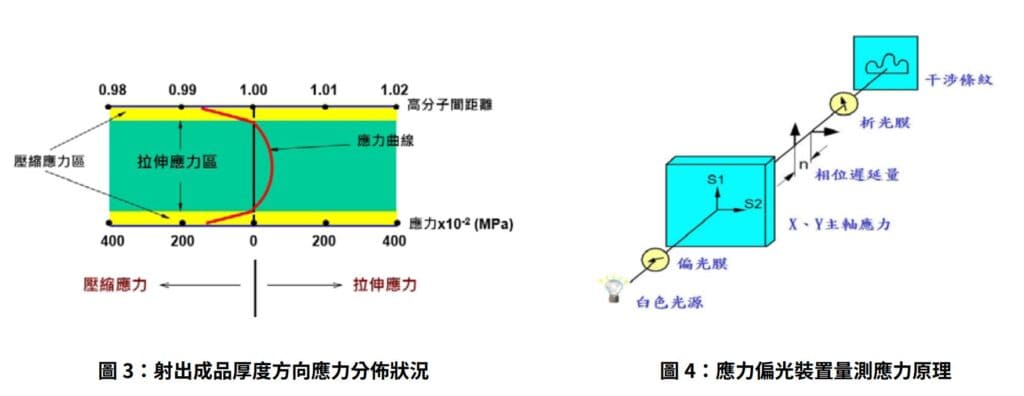
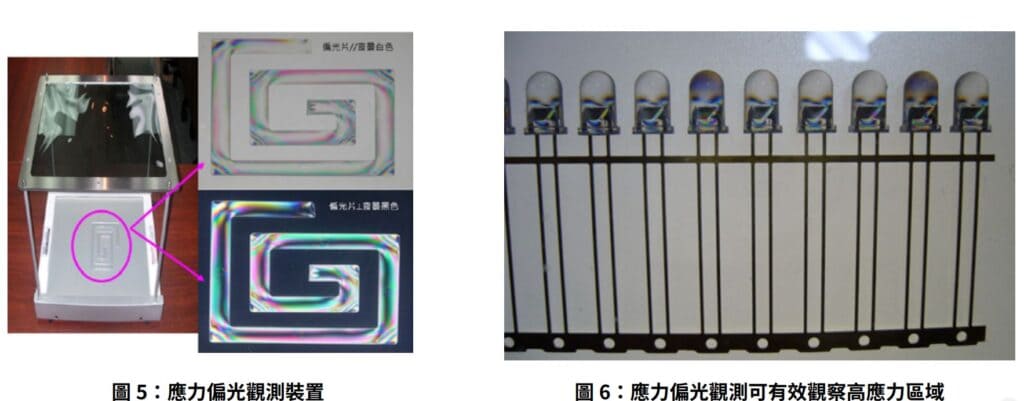
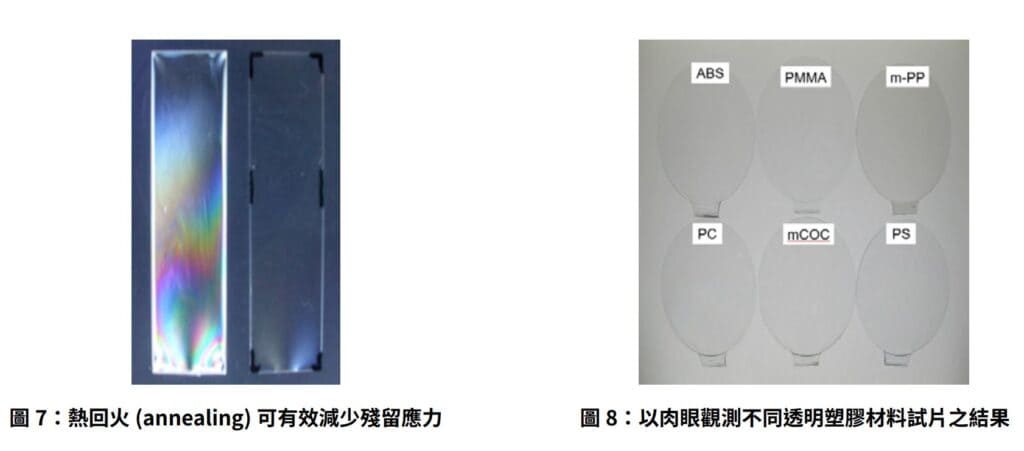
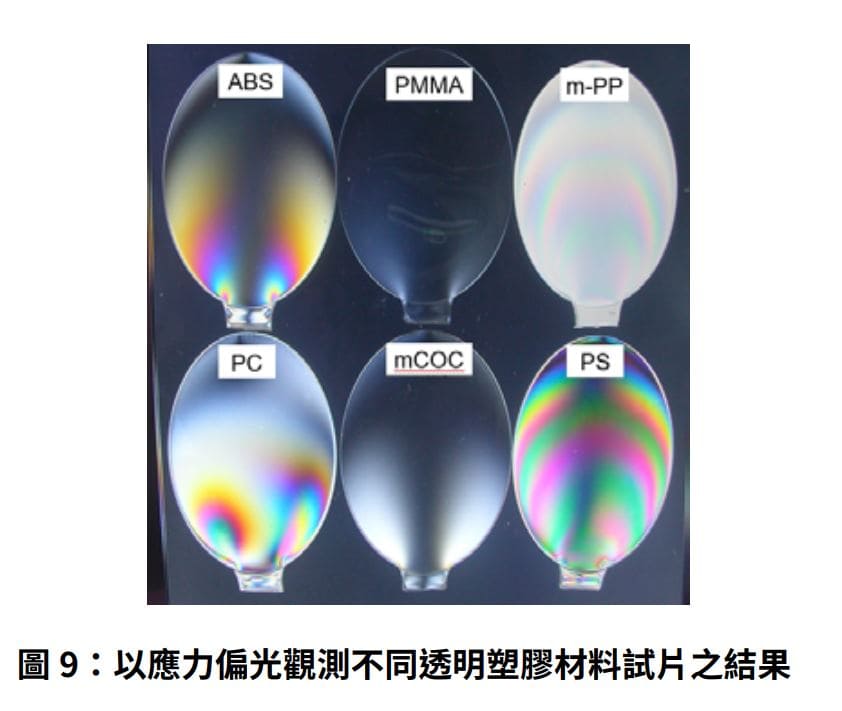
文章來源:SMART Molding雜誌