型創科技 / 王海滔 應用工程師
前言
目前全球都對汽車電動化發展普及持樂觀態度,同時考量節能減排政策與禁售燃油車的風向,汽車業需要成本更低、分量更輕的材料,從而提升燃料經濟性。美國法規將發佈平均燃油標準,將該數值限定在54.5英里每加侖,相較於當前的35.5英里每加侖,該數值的增幅高達60%。
碳纖維複合材料有望成為汽車結構件輕量化材料主線。相較於鋼材,碳纖維強度更高,分量也更輕,但其售價相對較貴。為便於未來大規模推廣應用,需要研發符合機械及安全性能的經濟型複合物,例如:聚丙烯及聚醯胺纖維等長碳纖維強化熱塑性樹脂等材料。
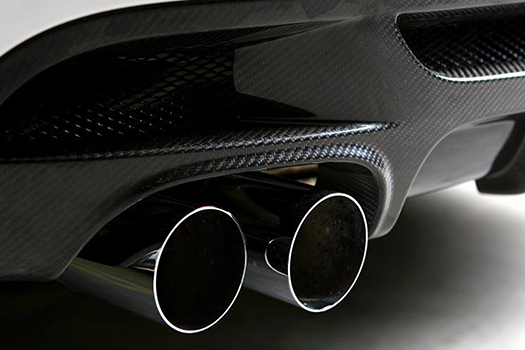
複合材料的特徵和優勢
強度高
高模量碳纖維複合材料強度可達鋼的五倍,鋁合金的四倍,鈦合金的三點五倍以上。
抗疲勞性能好
常用的碳纖維增強複合材料的疲勞極限是其抗拉伸強度的70%~80%,而大多數金屬材料僅能達到30%~50%
減振性能好
複合材料結構件的自振頻率高,同時複合材料中如加入高韌性的數值和橡膠基體還帶有振動阻尼特性。
各向異性及性能可設計性
纖維複合材料的性能與纖維的排列方向、鋪層次序和層數,以及成型方式都有關。通過設計與工藝的調整,可優化實現預定的功能要求。
耐磨、尺寸穩定性好
塑件得到了纖維的耐磨特性與尺寸穩定性。
綜上可知高分子材料由於纖維的加入,一方面其機械性能會得到提升,但同時也會面臨著纖維排列與預想不符、浮纖、孔洞、夾雜物、縫合線結合質量等缺陷問題。相較於普通塑膠材料(不含纖維),生產者判別複合材料製品是否合格,會更加複雜,需要全面檢測其微觀結構。
傳統複合材料測試方法
通常分成破壞性試驗和非破壞性試驗(無損檢驗)。破壞性試驗主要包括拉伸、衝擊、壓縮、彎曲、硬度等力學性能試驗,會對測試件的性能和外形破壞,因此成為破壞性測試。而無損檢測中,測試件性能和外觀不變,仍具有使用價值。
常用的工業無損檢測方式有雷射檢測、X射線檢測、電渦流式檢測、超聲波檢測、太赫茲檢測技術等等。以上原理均相似,利用光、電、聲、磁等物理方式接觸或穿透檢測塑件,並回收特定信號進行解析,得到我們需要的數據,如尺寸、密度、均勻性、內部結構或缺陷等。儘管目前無損檢測方法很多,但一般還不能做到在已知化學組成、製造過程及環境和載荷條件下準確預測出符合材料的剩餘使用壽命。
無損檢測促進碳纖維複合材料研發
當前碳纖維複合塑膠零部件的研發工藝,需結合考慮配件組裝並進行測試,是一個週期長且繁瑣的過程,延緩了車用碳纖維複合物的創新研發進程,同時從研發週期上降低了產品的成本效益。
通過模流分析軟體,使用精準測試的含纖材料數據,可以預測成型塑件內纖維方向及纖維長度的分佈。分析出來的模流結果再與無損檢測結果進行比對,從而驗證軟體與建模的精度。以利用高精準度的電腦試模結果,在開發前端就能「觀察」到塑件的內部結構進行優化,快速推進車用長碳纖維複合物的研發進程,實現成本降幅及性能增幅。
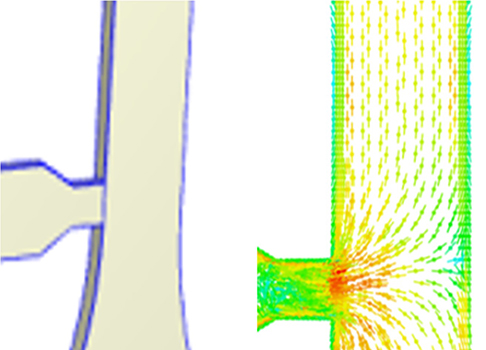
結語
隨著塑料種類的增多,塑料生產技術的不斷精進,在當下及日後的生產生活中,塑料將會發揮越來越大的作用。為了能高質量使用高分子材料,必須準確地掌握其物理力學性能及線上檢測功能機理的技術。無損測量技術正好滿足了這一技術要求,不僅僅是針對含纖複合材料,是促使所有塑料的傳統測試方法發生根本性的變革,使塑料質量控制達到一個新的水平。
文章來源:SMART Molding雜誌